
Hydraulic Steel Tubes
In the intricate world of engineering, where every component plays a crucial role, few materials stand as prominently as the EN10305-1 Hydraulic Steel Tubes. Whether silently supporting the framework of towering skyscrapers or orchestrating the graceful movements of heavy machinery, these tubes are the unsung heroes of modern industry. So, let's embark on a journey to unravel the secrets and significance of these remarkable creations.
Exploring EN10305-1 Hydraulic Steel Tubes:
The Backbone of Modern Industry

Hydraulics Steel Tubes
Mechanical Properties of the Tubes at Room Temperature
Delving into Characteristics:
Annealed, Phosphate, and Oiled Internally and Externally
Annealed Tubes
Annealing is a heat treatment process that imparts desirable properties to steel tubes, such as improved ductility and machinability. Annealed hydraulic steel tubes exhibit enhanced formability, facilitating easier manipulation during installation and maintenance.
Phosphate Coating
Phosphate coating serves as a protective barrier against corrosion, extending the lifespan of hydraulic steel tubes in demanding environments. It acts as a shield, safeguarding the integrity of the tubes even amidst exposure to moisture and harsh chemicals.
Internal & External Oil Coating
The application of internal and external oil coatings not only minimizes friction within the hydraulic system but also provides additional corrosion resistance. This dual-layered protection ensures prolonged service life and smooth operation, enhancing overall efficiency.
Enhancing Performance:
Understanding the Difference Between Seamless and Welded Hydraulic Tubes
Hydraulic tubes play a pivotal role in various industries, facilitating fluid power transmission in machinery and equipment. Understanding the manufacturing process behind these tubes is crucial for ensuring optimal performance and durability. One fundamental aspect to consider is the method of production: seamless or welded. Let's delve into the differences between these two techniques and their implications for hydraulic systems.

Seamless Hydraulic Tubes:
Pioneering Precision and Integrity
Seamless hydraulic tubes are crafted from a single billet, utilizing a meticulous manufacturing process that ensures superior precision and structural integrity. Unlike welded tubes, seamless ones do not feature weld-joins or seams along their length. This seamless construction offers several advantages:
01
Enhanced Durability and Strength
The absence of weld seams eliminates potential weak points, enhancing the overall strength and durability of seamless hydraulic tubes. This makes them particularly suitable for applications requiring high pressure and reliability.
02
Superior Fluid Flow Characteristics
Seamless tubes boast smooth internal surfaces, promoting uninterrupted fluid flow. This reduces turbulence and pressure drops within the hydraulic system, optimizing efficiency and performance.
03
Resistance to Corrosion and Fatigue
The seamless construction minimizes the risk of corrosion and fatigue failure, extending the service life of hydraulic tubes even in harsh operating environments. This makes them a preferred choice for critical applications where reliability is paramount.
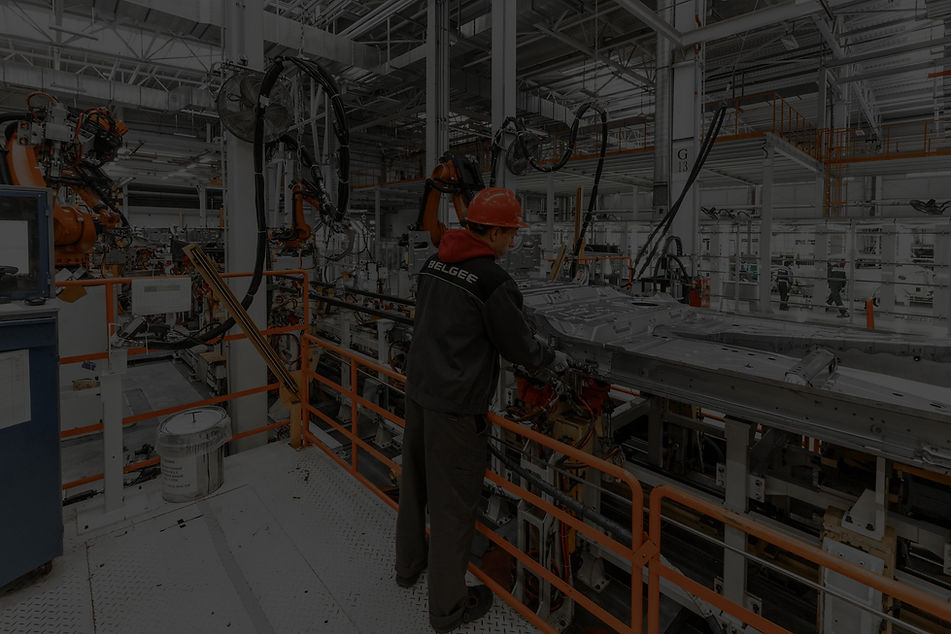
Welded Hydraulic Tubes: Balancing Affordability and Versatility
01
Potential Weak Points
Welded tubes feature weld seams along their length, which can serve as potential weak points vulnerable to cracking or failure under high pressure or stress conditions.
02
Limited Smoothness of Interior Surface
The welding process can result in irregularities along the interior surface of the tubes, leading to increased friction and turbulence in fluid flow. This can affect the overall efficiency of the hydraulic system.
03
Susceptibility to Corrosion
Welded joints are more prone to corrosion compared to seamless construction, especially if not properly treated or coated. This can compromise the integrity of the hydraulic system over time.
In contrast to seamless tubes, welded hydraulic tubes are manufactured by welding together strips or plates of steel. While they offer certain advantages, such as cost-effectiveness and versatility, welded tubes also have limitations:
Choosing the Right Option for Your Application
When selecting hydraulic tubes for a specific application, it's essential to consider factors such as operating conditions, pressure requirements, and budget constraints. While seamless tubes offer unparalleled strength and performance, welded tubes may be more suitable for less demanding applications where cost is a significant consideration.
In conclusion, understanding the distinction between seamless and welded hydraulic tubes is crucial for optimizing the performance and longevity of hydraulic systems. By choosing the right type of tubes for your application, you can ensure smooth operation, minimize downtime, and maximize efficiency in your machinery and equipment.
Manufacturing Process for DIN EN 10305 Tubes
Overview of Tubes Production
Crafting DIN EN 10305-1 and DIN EN 10305-4 tubes involves a meticulous manufacturing process to uphold their precision and excellence. Below, we delve into the key stages:
Tubes Formation: Selecting Quality Steel
Initiating with premium-grade steel, tailored lengths are crafted through precision cutting. These steel sections undergo heating and piercing to forge the foundational hollow tubes structures.
​
​
Cold Drawing: Enhancing Dimensional Precision
The next phase entails subjecting the raw steel to cold-drawing procedures. Through successive passage via dies, the steel is tapered, refining its diameter and achieving precise dimensions. This method not only guarantees exact sizing but also bolsters the tubes' mechanical attributes, ensuring tight tolerances and a sleek surface texture.
​
Heat Treatment: Reinforcing Strength and Hardness
Augmenting the tubes' robustness and durability involves a meticulous heat treatment regimen. Here, the tubes are heated to specific temperatures before undergoing rapid cooling, a process known as quenching. This controlled cooling imparts the desired mechanical resilience to the tubes.
​
Surface Finishing: Achieving Exceptional Quality
A pivotal aspect of DIN EN 10305-1 and DIN EN 10305-4 tubes is their superior surface finish. Employing techniques like pickling, phosphating, or passivation, depending on application requisites, ensures the elimination of impurities and the creation of a seamless, corrosion-resistant surface.


Addressing Concerns:
Frequently Asked Questions
01
What are the benefits of using ST 52.4 tubes over ST 37.4 tubes?
ST 52.4 tubes offer superior strength and durability, making them suitable for applications requiring high performance under heavy loads. In contrast, ST 37.4 tubes provide cost-effective solutions without compromising on reliability.
03
Why is phosphate coating essential for hydraulic steel tubes?
Phosphate coating acts as a protective barrier against corrosion, extending the lifespan of hydraulic steel tubes in harsh environments. It ensures the integrity of the tubes, even in the presence of moisture and chemicals.
02
How does annealing enhance the properties of hydraulic steel tubes?
Annealing improves the ductility and machinability of steel tubes, making them easier to manipulate during installation and maintenance. It also relieves internal stresses, enhancing the overall resilience of the tubes.
04
What role do internal & external oil coatings play in hydraulic systems?
Internal and external oil coatings minimize friction within the hydraulic system, improving operational efficiency and reducing wear and tear. Additionally, they provide an added layer of corrosion resistance, prolonging the service life of the tubes.
05
Where are hydraulic steel tubes commonly used?
Hydraulic steel tubes find applications across various industries, including automotive, machinery manufacturing, aerospace, and defense. They are integral components in hydraulic systems, ensuring the seamless transmission of fluids and the smooth operation of machinery.
Summary
As the backbone of modern industry, EN10305-1 Hydraulic Steel Tubes embody resilience, precision, and reliability. From towering skyscrapers to the depths of the ocean, these tubes silently enable the smooth functioning of our technological landscape. With their robust construction and versatile capabilities, they continue to shape the course of progress, one hydraulic system at a time.